FAQ
Frequently asked questions
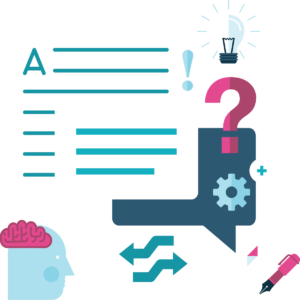
Below you can find more information about some of the methodology we use.
Process improvement methodology for increasing quality, reducing defects, understanding variation & improving process capability. Developed in electronics (by Motorola in 1980s) & originally used in manufacturing Six Sigma is now widely applied across all business processes and all sectors. Principles of Six Sigma are
- Start with the customer – what are their critical to quality requirements (CTQs)
- Understand how well our processes meet the CTQs
- Understand and reduce variation
- Undertake improvements in a systematic, data driven way
- Involve and equip the people in the process
Improvement methodology focussed on reducing waste and non-value added activity and improving flow. Increases efficiency, productivity, effectiveness and responsiveness of business activities whilst also improving quality and customer service. Basic concepts originally developed Toyota (automotive manufacturing) but Lean thinking and Lean process improvement is now widely used across all business processes & sectors.
Principles of Lean are
- Understand the customer and their perception of value
- Identify and understand the value stream for each process and the waste within it
- Enable the value to flow
- Let the customer pull the value through the processes, according to their needs
- Continuously pursue perfection (continuous improvement)
Combines the best of the Lean & Six Sigma toolkit in a single improvement project methodology (DMAIC). Allows a common business – wide improvement approach to be used to tackle all sorts of process & business problems whether they are due to ‘variation and defects’ or ‘waste & flow’.
Structured project methodology for Lean Six Sigma improvement projects.
Five project phases – each phase has a clear set of deliverables and tools to support effective project delivery:
Define – Define and scope the problem.
Measure – Understand how the current process works and collect relevant data/information to help better understand the problem
Analyse – Analyse root causes of the problem
Improve – Identify and prove solutions to fix the problem
Control – Implement the solutions in a way to ensure improvement is sustained
Structured project methodology for Lean Six Sigma design projects (where significant change is required & improvement of existing processes is not appropriate. In this situation you are looking to ‘start with a (nearly) blank sheet of paper’)
Five project phases – each phase has a clear set of deliverables and tools to support effective project delivery:
Define – Define and scope the problem.
Measure – Understand the customer needs and translate into target performance goals for the solution
Analyse – Analyse alternative solution concepts and select the best
Design – Develop and test detailed design(s) for the new solution
Validate – Implement the solutions and validate
A business management approach focussed on delivering improved customer value and increased profitability through driving excellence into all critical aspects of business operation. Traditionally the focus of manufacturing companies, the ideas of operational excellence are now being applied across all types of business and sectors as organisations compete for highly demanding customers. Operational excellence is achieved through a focus on People, Process, and Data.
Lean Six Sigma is the most widely used improvement methodology for achieving Operational Excellence.
Green Belt – Teaches the DMAIC method and broad suite of improvement tools (excluding heavy stats and data analysis). Appropriate for anyone leading improvement projects.
Black Belt – Builds on Green Belt Training. Includes advanced data analytics, data modelling, and DOE. Also Change Leadership skills. Appropriate for anyone leading ‘data rich’ improvement projects or more complex DMAIC projects.
Master Black Belt – Most advanced level of Lean Sigma Training. Appropriate for anyone leading a broader Lean Six Sigma Improvement programme across a business (or part of the business). Master Black Belts typically act as ‘internal consultants’ managing large strategic projects & working alongside the business leadership to drive Lean Sigma and Operational Excellence into the organisation.
Individuals can be certified to a particular belt level by an external accreditation body e.g. BQF (British Quality Foundation).
Certification requires – attending appropriate training; passing an exam; completing an improvement project; presenting the project to a licenced Assessor.
Kaizen is Japanese word that means ‘improvement’. Kaizen event is a term widely used for a rapid improvement event during which improvement is delivered over (typically) a 5 day burst rather than a Green Belt or a Black Belt project which may take 6 – 9 months (depending on project scope and complexity)
Kaizen Events still use the DMAIC methodology in a more compressed form.
Kaizen Events are not appropriate for solving all types of process problems but can be very powerful in the right circumstances.
CI Describes a widely accepted approach to business improvement which focusses on breaking problems down into ‘bite size’ chunks in such a way that allows lots of smaller tightly scoped improvement projects to be delivered which, when taken together, result in significant transformation over time.
This is the alternative to the more traditional ‘big project/big bang’ approach.
Continuous improvement is at the heart of Operational Excellence and the Lean Six Sigma approach.
Our Performance Management System is a structured framework for engaging everyone in OpEx through their daily activities.
Sustainable and successful OpEx requires:
- Clear business direction to ensure effort is focussed on the right things
- Effective delivery of improvements?
- A culture of problem-solving and continuous improvement.
Our Performance Management System delivers:
- Top-to-bottom alignment on direction and priorities?
- Visible performance measures aligned across the business
- Decision-making and accountability driven to the right level
- Effective problem solving with Leaders as coach.
Implementation of our Performance Management System focusses on:
- Leader Standard Work
- Tier Management & Review
- Visual Performance Management
Data exploration and analytics software. Highly visual and intuitive to use. Also very powerful data & Text analytics & DOE platforms.
Demonstrated to improve Black Belt productivity and benefits delivery by >30% compared with other widely used alternatives (e.g Minitab).
Exclusively the data analytics software Process Insight use with their clients.