Case studies
See how we have helped clients across many sectors solve their business problems and deliver tangible benefits
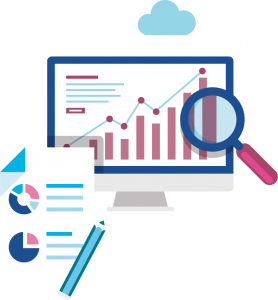
The Pisa plant is one of Saint-Gobain Glass’s oldest glass manufacturing facilities. With a very broad product range the business carried large inventory of products of different colours, thicknesses, coatings and sizes (>1200 SKUs). The nature of the glass manufacturing process necessitates long campaign lengths to achieve stability. With manufacturing lead times greatly in excess of customer lead times the supply chain strategy was to stock against forecast. This required two large warehouses on site for plus satellite warehouses across Italy .
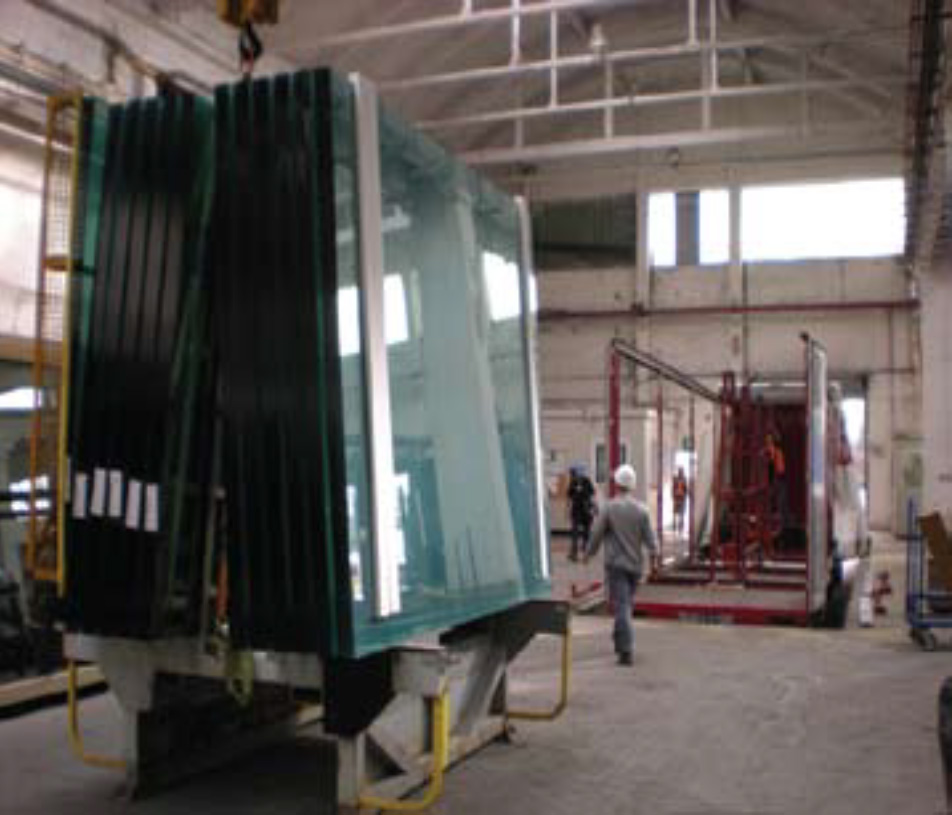
The challenge was to find a way of dramatically reducing the inventory to provide space for the installation of a new coater and allow the sale of surplus land to pay for it. An across the board percentage inventory reduction was unlikely to succeed – previous stock reduction efforts had resulted in temporary reductions followed by unexpected stock outs and then a gradual drift back to high stocking levels.
- Analysis of demand patterns and demand variability (by SKU family)
- Data analysis to focus in on critical product families and value streams
- Value Stream Mapping (VSM) project selection Kaizen event with team to identify high impact improvement projects
- Implementation of new production planning rules and buffer stock levels based on runners/repeaters/specials
- Warehouse layout redesigned
- Loading operations simplified
- Reduction in inventory levels by more than 20% without any adverse customer impact
- Reduction in storage area by more than 30%
- Validated savings of €600,000
- Broad engagement of workforce in Lean Kaizen improvement processes
A longer version of this case study appeared in UK Excellence Magazine
Share on facebook
Facebook
Share on twitter
Twitter
Share on linkedin
LinkedIn